UCI Trains Undergrads in Clean Room Skills
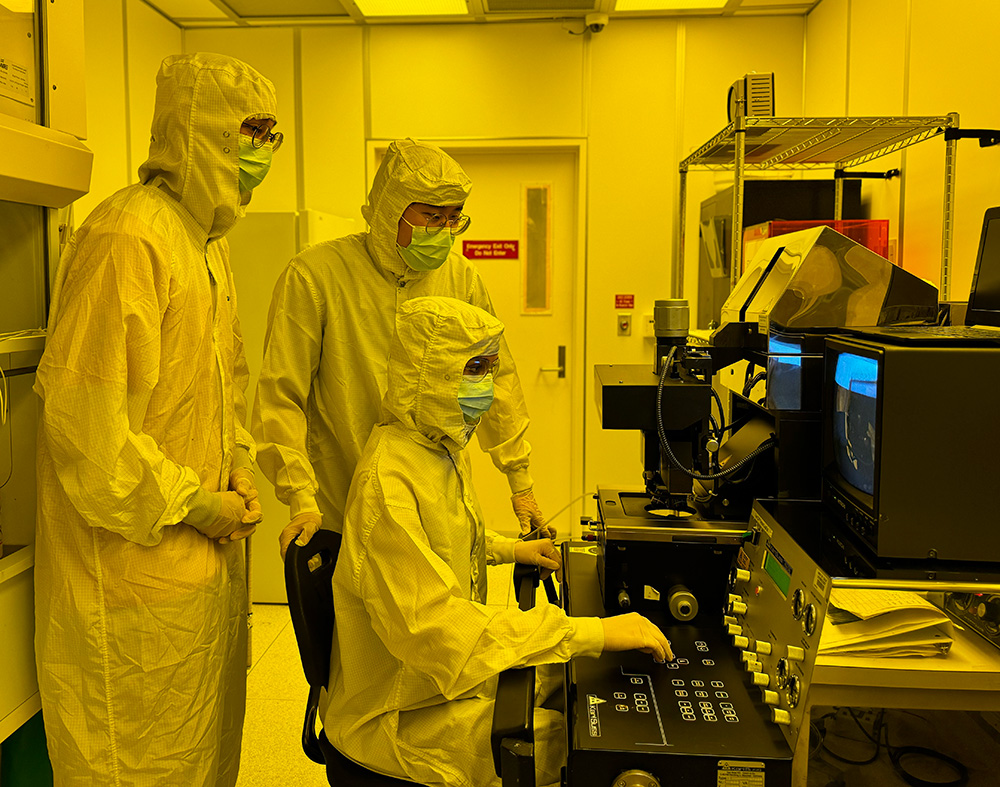
Students work on an aligner for photolithography in UCI’s clean room.
Sept. 18, 2024 - UC Irvine just launched a new class that gives undergraduate engineering students a rare opportunity to learn clean room skills. Clean rooms are nearly dustless labs where semiconductor chips, microsensors and microdevices are made.
UCI’s pristine 15,000 sq. ft. facilities, which include Integrated Nanosystem Research Facility (INRF) at Engineering Gateway and Bio-Organic Nanofabrication (BiON) at CalIT2, strictly limit contaminants as filtered air preserves the integrity of the microfabrication processes. Visitors must wear head-to-toe coverings to protect the clean environment from dust and other outside pollutants.
Hung Cao, associate professor of electrical engineering and computer science, says a clean room class is very rare for undergraduates in the U.S. as usually only Ph.D. students receive this highly skilled training. Students clamored for this unique opportunity. The 199 Engineering Microfabrication class saw 200 students sign up on the first day for a program that takes just 12 students.
The U.S. is trying to catch up with Asia in its semiconductor manufacturing. Cao said the class is the Samueli School’s contribution to making the U.S. more competitive in the chip war.

Biomedical engineering student Kristin Hagen shows off the Anteater sensor she made.
The pilot program was launched in spring 2024 and Cao just finished teaching a second session this summer. The six-week program trains 12 students in the process of using six key tools for microfabrication. During that time, the students made a 2 cm x 2 cm Anteater microsensor that can distinguish between different fluids and gases via impedance measurement with the Anteater’s nose.
The CHIPS and Science Act brings much government funding and support to the semiconductor industry. Isaac Mays, a second-year UCI electrical engineering student, said those future job opportunities are why he wants to pursue a semiconductor fabrication career.
“Dr. Cao’s research is very well-known and notable, and I wanted to be in the first group that are trained and have access to that equipment,” Mays said. “I actually knew nothing going into it and now I’m sitting here with a microsensor I made myself, which is really awesome. It’s a seven-step process – almost like baking a cake.”
First, an insulation layer of SiO2 (glass) is formed on top of a silicon wafer. Then metal patterns are made using thin-film deposition, lithography and etching. Next, another insulation layer is made using a high-precision aligner. Then, the individual microsensors are diced and characterized.
This summer, Camilo Velez Cuervo, assistant professor of mechanical and aerospace engineering, also taught the students how to use dedicated tools to measure the performance of their sensors in his lab.
“I really wanted to enroll in this class because I’ve been looking for an opportunity to learn about semiconductors. They’re such a hot commodity on the market, that whenever I tried to enroll in anything related to them, it’d be full in less than 10 seconds,” said Amin Mansouri, a mechanical engineering senior.
Mansouri does research in fuel cells under Professor and Chancellor’s Fellow Jack Brouwer at UCI’s National Fuel Cell Research Center, a global leader in fuel cell technology. He said the clean room class has inspired him with ideas to integrate microfabrication skills in his fuel cell research.
The program doesn’t just appeal to students eyeing the chip industry, but also a broad spectrum of future engineers who need micro/nanofabrication skills. “I’m really interested in microfluidics,” said biomedical engineering student Kristin Hagen. “Clean room microfabrication is a really big part of making devices to model physiological systems.”
The clean rooms develop micro- and nanodevices and contain tools that can perform ultra-small-scale fabrication on materials such as polymers, hydrogels, collagens, proteins and even living tissue.
“I learned a lot about different materials you can use and the different strategies to make the device you want,” Hagen said. “When you’re working on such a small scale, you have to be very strategic about what you do.”
One of the tenets of UCI’s Samueli School is to provide hands-on learning experiences for future Anteater engineers. “I enjoyed taking Dr. Cao’s class because it let me get outside of a lecture hall and away from theory and get more hands-on practical experience inside the clean room here at UCI,” said Christian Cao, a biomedical engineering-premed junior. “The experience in the clean room really helped me develop skills for my specialization in microfabrication.”
The pilot undergraduate program in the clean room has become an excellent way to equip and inspire future engineers. Hung Cao says he hopes other universities will look to host similar programs so the U.S. can build a competitive workforce in the semiconductor industry.
- Natalie Tso