UCI Engineer Uncovers Dislocation Patterns in Deformed Materials
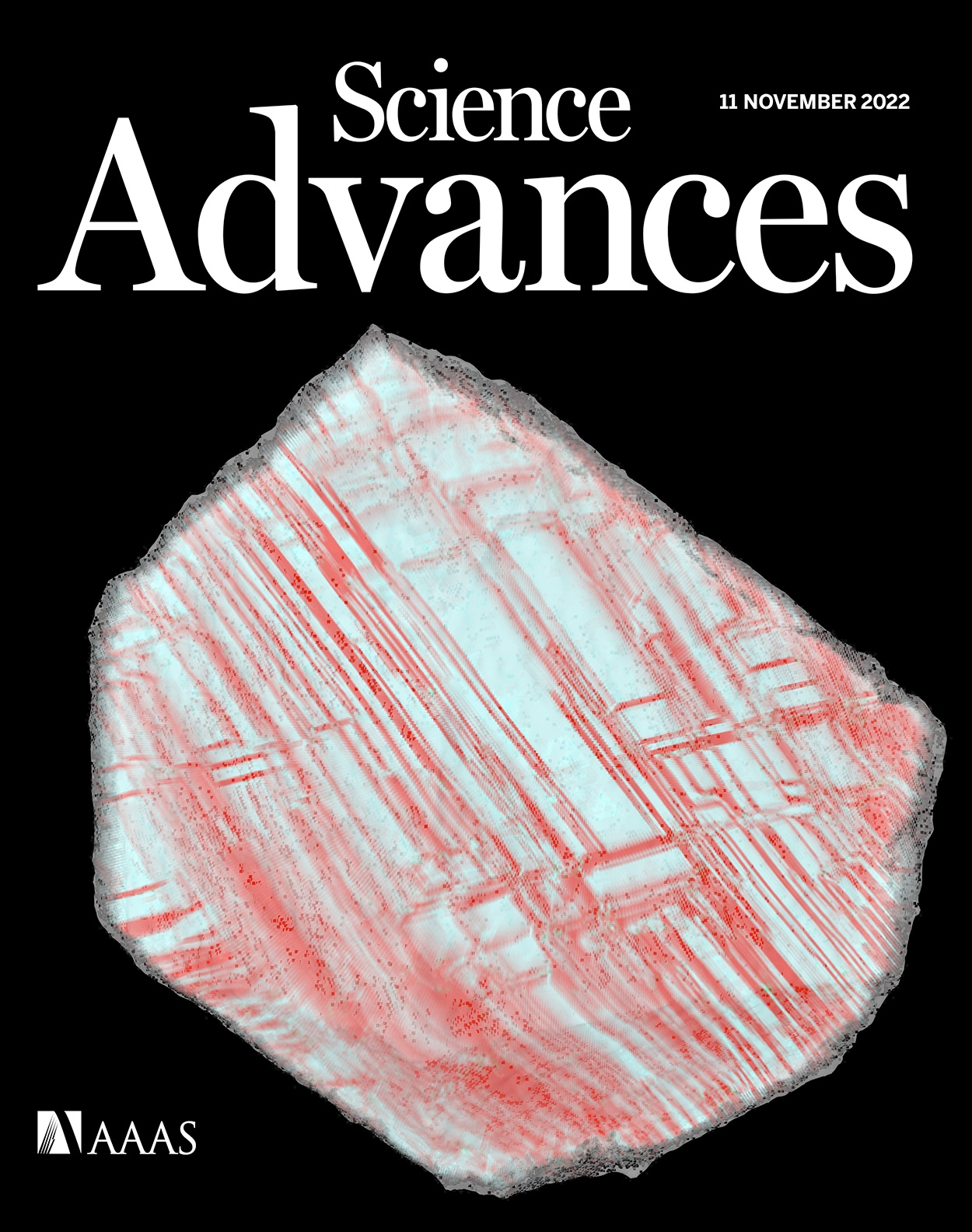
Nov. 9, 2022 - Did you ever wonder why your spoon, which bent while scooping ice cream, could never be perfectly put back to its original shape? It has to do with plasticity, a material’s permanent deformation in response to mechanical force, in this case stainless steel.
Penghui Cao, assistant professor of mechanical and aerospace engineering, studies extreme performance of materials and how they behave in extreme conditions such as high strain rate, high temperatures and high radiation exposure. He says that by understanding the microstructures and dislocation patterns in a deformed material, scientists and engineers can design and fabricate stronger materials with tunable mechanical behaviors. Leveraging large-scale modeling at the atomic level and a new structure identification algorithm, he has identified three distinct dislocation patterns that occur in metals that have changed shape. This work is reported today in Science Advances, Issue 45, featured on the cover.
“Even with advanced microscopy, understanding dislocation structure evolution is challenging because of the inability to in-situ track dislocations in three-dimensional bulk materials during deformation,” said Cao. "Depending on the stretching direction, the dislocation lines intriguingly self-organize in different ways, manifesting as three distinct patterns."
In common metals such as aluminum, copper, gold and silver, only four non-parallel crystallographic planes exist for movement to happen. Cao found that when only one plane is activated during stretching, dislocation lines navigate on parallel planes and rarely interact with one another. While two intersecting planes are activated, dislocations collide with each other and form a gridded pattern. If all slip planes become active, dislocations intersect and emerge as a three-dimensional network.
The findings, addressing deformation microstructure and maximum strength, will facilitate material design strategies for achieving ultimate mechanical performance. High strength and tough alloys used in vehicles, for example, could reduce the component weight without compromising safety, improving efficiency in automobiles. Tunable material performance would benefit a variety of other technology applications, particularly in aerospace and nuclear industries as well.
“By simultaneously controlling texture and chemical order, we can promisingly approach the maximum strength materials inherently hold at the level of polycrystals,” said Cao.
The research was funded by the Army Research Office and Department of Energy.
– Lori Brandt