NSF Funds Research on Lower-Temperature, Renewable Cement Manufacturing Process
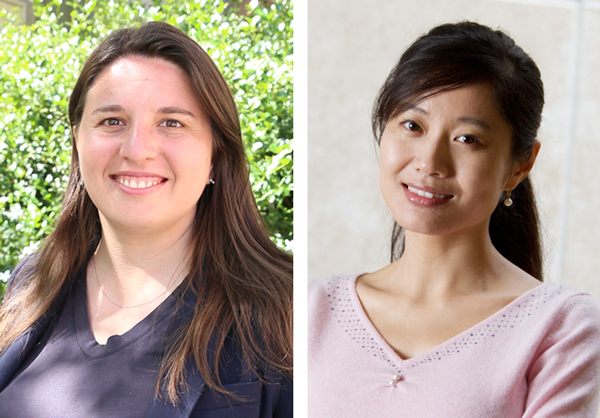
Iryna Zenyuk (left) and Mo Li are working together on an NSF-funded project to assess the feasibility of a lower-temperature, renewable cement manufacturing process.
Sept. 11, 2020 - Two Samueli School engineering researchers have received a Future Manufacturing Seed Grant ($500,000) from the National Science Foundation for their project to substitute an electrochemical process for the combustion process in the manufacturing of cement, which would significantly reduce its manufacturing energy input and carbon footprint.
The current manufacturing process for Portland cement, the most common ingredient used in structural concrete, requires temperatures above 1400 degrees Celsius, using heat provided by the combustion of fossil fuels. This method, which has not fundamentally changed over the past 140 years, accounts for 5% of worldwide industrial energy consumption and is responsible for 5-8% of human-generated global CO2 emissions.
Principal investigator Iryna Zenyuk, associate professor of chemical and biomolecular engineering, and co-principal investigator Mo Li, associate professor of civil and environmental engineering, are proposing a new, chemical pathway to producing cement with a much-reduced carbon footprint and energy usage, while enabling the use of electricity from non-fossil fuel and renewable resources.
The project will transform cement manufacturing by changing the chemical process of converting calcite (i.e. limestone) to calcium oxide via calcium hydroxide formation using an electroyzer, as opposed to direct limestone calcination in a conventional fossil-fuel fired kiln.
“We hope to open the door to eco-manufacturing of cement by using renewable electricity from wind and solar power generation,” said Zenyuk, who is also an associate director of the National Fuel Cell Research Center at UC Irvine. “Difficult-to-decarbonize sectors, such as steel and cement manufacturing, and air and heavy-duty transportation, require novel approaches to transform them into net zero-emission. I am thankful to NSF for funding this original manufacturing concept.”
The researchers will provide fundamental insights into the new lower-temperature chemical process of cement manufacturing by assessing the scalability of the electrochemical method and its overall efficiency; comparing the chemical composition, reaction chemistry and resulting properties of this new approach to those of conventional approaches; and quantifying the new process’s economic and environmental advantages.
“Global cement production has increased rapidly since World War II but has followed a traditional approach established in the early 19th century,” said Li, who directs UCI’s Infrastructure Materials Research and Advanced Manufacturing Lab. “We aim to enable a clean, electrochemically based cement-manufacturing approach, demonstrate the new concept’s feasibility and build a multidisciplinary research/industry team to realize the future manufacturing of cement.”
The project also includes broader elements aimed at preserving U.S. leadership in efficient, low-carbon-emission manufacturing of cement while developing a highly trained workforce skilled in renewable, energy-efficient technologies.
The project is jointly funded by NSF’s Division of Chemical, Bioengineering, Environmental and Transport Systems; Division of Chemistry; and Division of Undergraduate Education.
– Lori Brandt