Building a Better Tomorrow
Professor Mo Li is engineering the materials and methods that will build the roads, bridges, buildings, energy infrastructure and defense structures of the future.
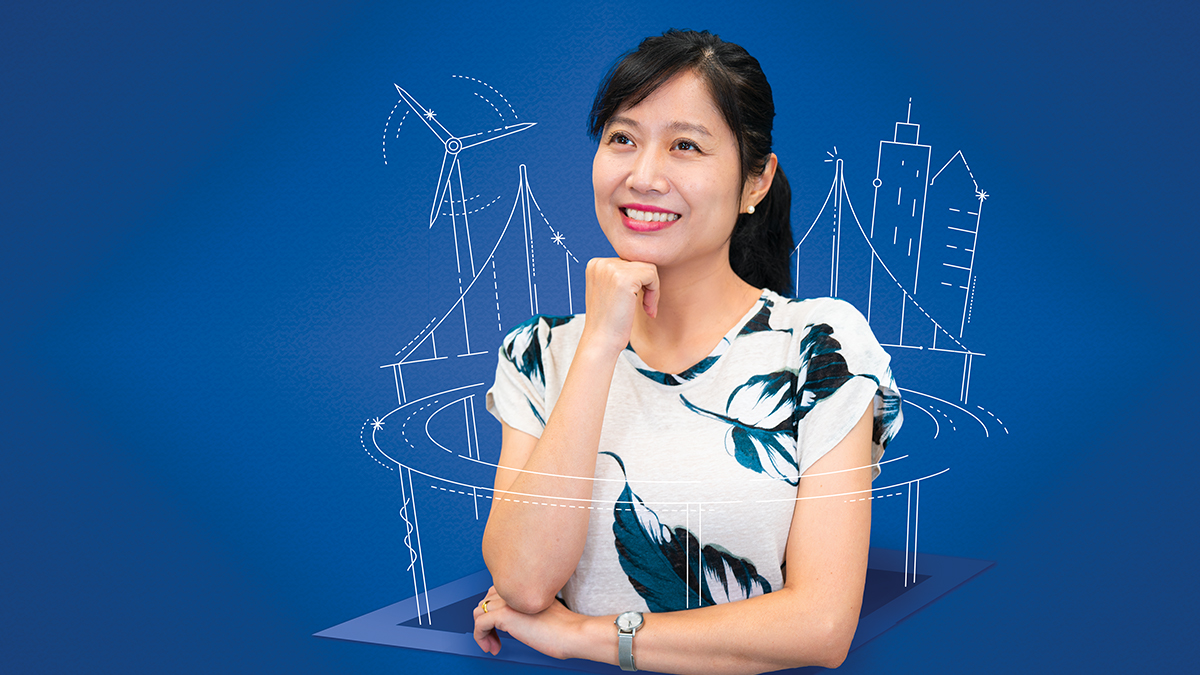
November 19, 2019 - Concrete is the most heavily used man-made material on earth.
Mo Li, Ph.D., UC Irvine associate professor of civil and environmental engineering and associate professor of materials science and engineering at the Henry Samueli School of Engineering, sees the tremendous impacts of the mass consumption of concrete on the economy, environment and society. In her view, if the materials used to build the world around us can be made stronger, smarter and more resilient, the whole world aims to benefit. To that end, Li works on numerous research projects to develop next-generation infrastructure materials and technologies for building safer, more durable and energy-efficient structures.
Groundwork
The way things are built has always fascinated Li.
“I was always interested in architecture and buildings and structures,” said Li. “So that’s how I picked civil engineering for my undergraduate studies. Not many girls picked this major at the time.”
Throughout her undergraduate and M.S. studies, Li’s background was more in structural engineering – like the design and analysis of bridges and buildings – but while working on her Ph.D., her work started to focus on structural materials as she saw the impact of materials innovation on civil, energy and defense structures.
“Every time we have major changes in human history, there’s always some advancement in materials,” said Li. “Think the Bronze Age, the Iron Age, the Industrial Revolution, and the ‘silicon age’ of the 21st century.”
The annual consumption of concrete is greater than all of the other engineering materials combined. Because such huge quantities are used, and the fact that cement production requires a significant amount of energy and contributes to about 8 percent of global CO2 emissions annually, sustainability has been a main focus for Li.
“Can we radically improve concrete performance while minimizing the environmental footprint and usage of energy and nonrenewable resources?” said Li. “This would lead to a more sustainably built environment, increase energy and national security, and greatly benefit our society and future generations.”
Material Limitations
In parts of Europe and Asia, the oldest structures were made with stone or masonry because those were the available construction materials at the time. Arches were often used in the construction of bridges and cathedrals, not only because they were aesthetically pleasing, but because the arch structure allows materials to withstand greater forces.
Masonry, like concrete, is very strong under compression – or inward, pushing forces. However, masonry and concrete are much weaker, or brittle, under tension – or outward, pulling forces.
With the advent of steel, structures did not have to rely as heavily on specific architectural designs like arches because steel could provide the strength and ductility under tension that earlier materials lacked. Steel-reinforced concrete – combining the tensile advantage of steel and compressive advantage of concrete – has become widely used in the constructions of bridges, buildings, roads, dams, pipelines, sea walls, nuclear power plants, wind turbine towers and foundations, and defense structures.
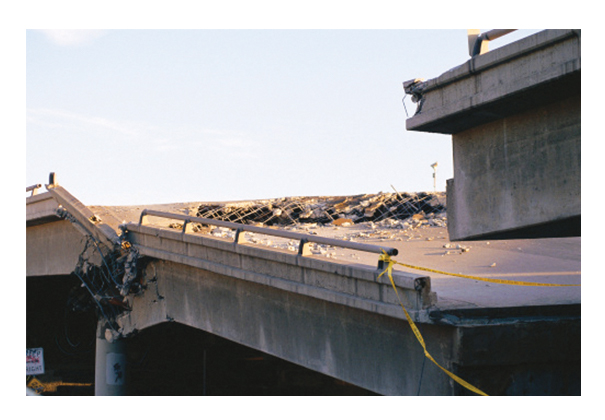
The damage left behind from earthquakes are a reminder of the limitations of today’s steel-reinforced concrete structures.
Despite all these advancements, modern structures and infrastructure are still susceptible to aging and deterioration under service conditions, and safety concerns under extreme events. Under daily mechanical and environmental stressors, concrete cracks and deteriorates, becoming more vulnerable to aggressive ions that cause steel reinforcement corrosion. Under hazard events such as earthquakes, hurricanes, fires or impact loads, buildings can experience catastrophic failures. In the case of earthquakes, concrete undergoes deformations that it cannot fully withstand, causing concrete failure and compromising the safety of the structure.
The root cause of these failures is due to the material limitations of concrete, namely its brittleness under tension. This can lead to a number of durability and safety issues, according to Li, which is why her Ph.D. focused on reengineering concrete so that it performs in a ductile and strong manner under tension, like metal.
Infrastructure Health
After her Ph.D., Li began her independent work as a faculty member and started to think about how to diagnose the health of aging infrastructure.
Although inspections of large structures, like bridges, are done by experienced engineers, little more than visual inspections of exposed surfaces are conducted because that is all that can be done.
To address this problem, many have thought to install sensors to monitor a structure’s health. The problem, Li states, is that these sensors only monitor the limited locations in which they are installed and do not measure what is going on between the sensors within the structure. The sensors do not directly measure damage either. Additionally, these sensors are expensive, difficult to maintain and do not last long.
Monitoring the health of structures goes beyond bridges, too. The Department of Energy (DOE) wanted to fund research that could ensure the integrity of nuclear power plants and spent nuclear fuel storage systems. The spent nuclear fuel storage structures, particularly, need to last many hundreds of years – much longer than the average bridge lifespan.
Li has a solution to this problem – which was funded by the DOE – and has filed a patent with help from Michael Harpen, licensing officer at UCI Beall Applied Innovation. Her approach is twofold.
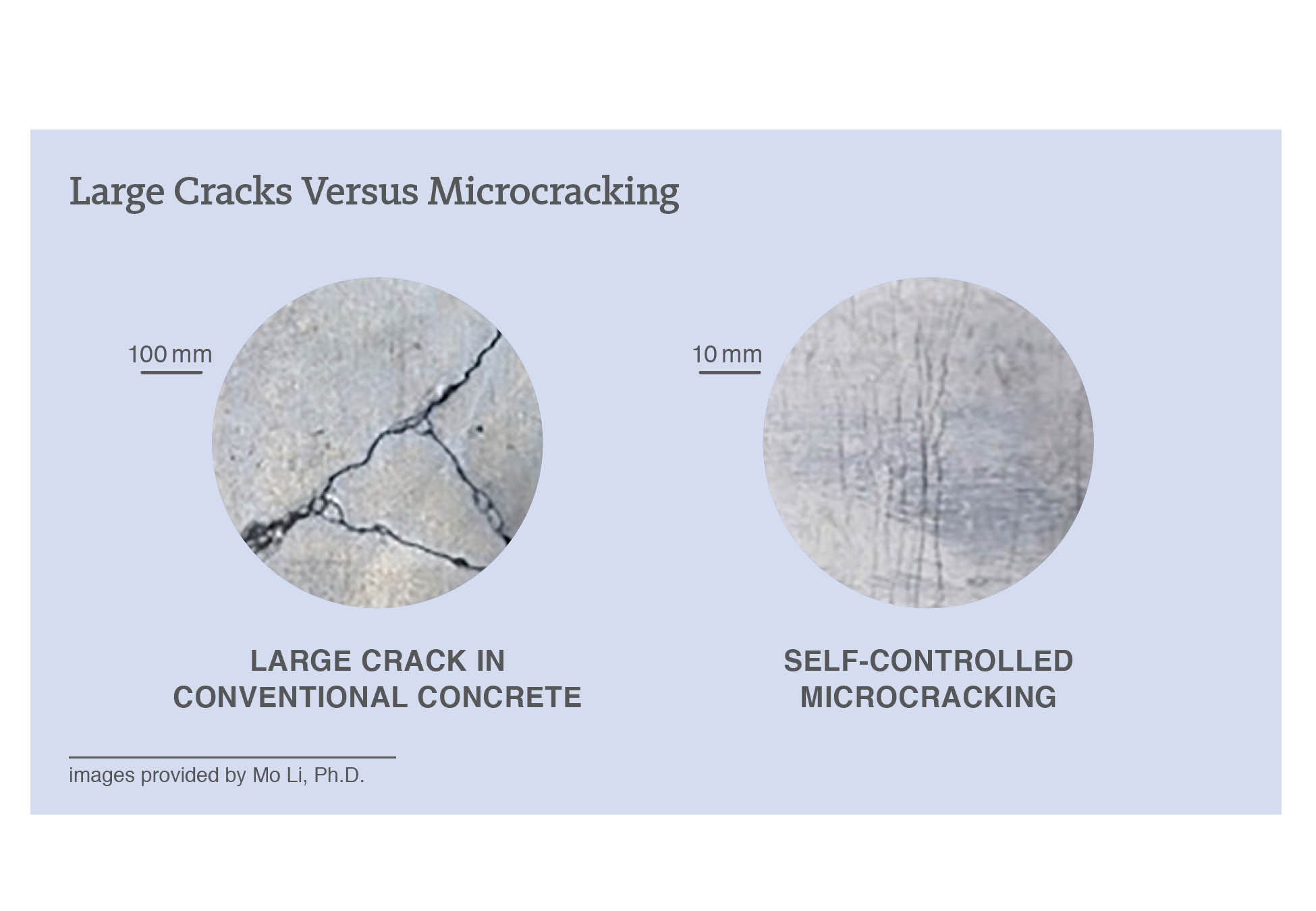
The first part is a new, durable and highly damage-tolerant concrete that is able to dissipate energy to withstand greater loads and, when under large deformation, produces only self-controlled microcracking with extraordinary ductility that maintains its structural integrity instead of larger fractures.
The second part is that the damage-tolerant concrete is also encoded with novel electromechanical properties to function as a spatial sensor within structures. This multifunctional concrete, coupled with advanced frequency-difference impedance tomography techniques – both developed in Li’s lab – offers a solution for monitoring a structure’s health. Through electrical probing only from the structural surfaces, damage and deterioration everywhere within reinforced concrete structures can be visualized in three dimensions with spatially continuous resolution. This approach does not require installation of sensors; rather, it makes structures behave as sensors themselves. This material is referred to as a self-sensing structural material.
By understanding how the nanostructures and microstructures of concrete respond to a wide frequency range of electrical currents, Li and her team tailor the nanostructures and microstructures of concrete to achieve a strongly coupled electromechanical behavior. This allows mechanically and chemically induced strains, cracks and damage to be identified, located and visualized through electrical probing under different electrical frequencies. With the information gathered, a comprehensive approach to inspections would be possible and result in a more thorough understanding of a structure’s health and integrity. Engineers could more accurately decide if the structure needs to be repaired or retrofitted or if it is close to failure and might collapse.
Stronger, Better, Faster, Taller
As if developing new multifunctional concrete and advanced imaging technologies to assess and protect structural health wasn’t enough, Li is also busy with other research projects that will improve the structures of tomorrow.
One such project centers on sustainability. Li is developing new self-healing cements from industrial waste – like slag, fly ash and metakaolin – and minerals that are abundant on earth. These byproducts are readily available, so the difficulty comes in making sure the resulting cements have the correct chemistry and mechanical properties – durable enough to be suitable alternatives to traditional cement. From there, Li also aims to create a new class of geopolymer-based infrastructure materials that can robustly and repeatedly heal and remove their own damage during infrastructure service life. As an alternative to cement, geopolymer production per metric ton only consumes 29 percent as much energy and generates 18 percent as much CO2. The self-healing functionality further reduces repair and maintenance needs, thus minimizing life-cycle costs, energy consumption and carbon footprint. This can lead to vast opportunities for sustainable development.
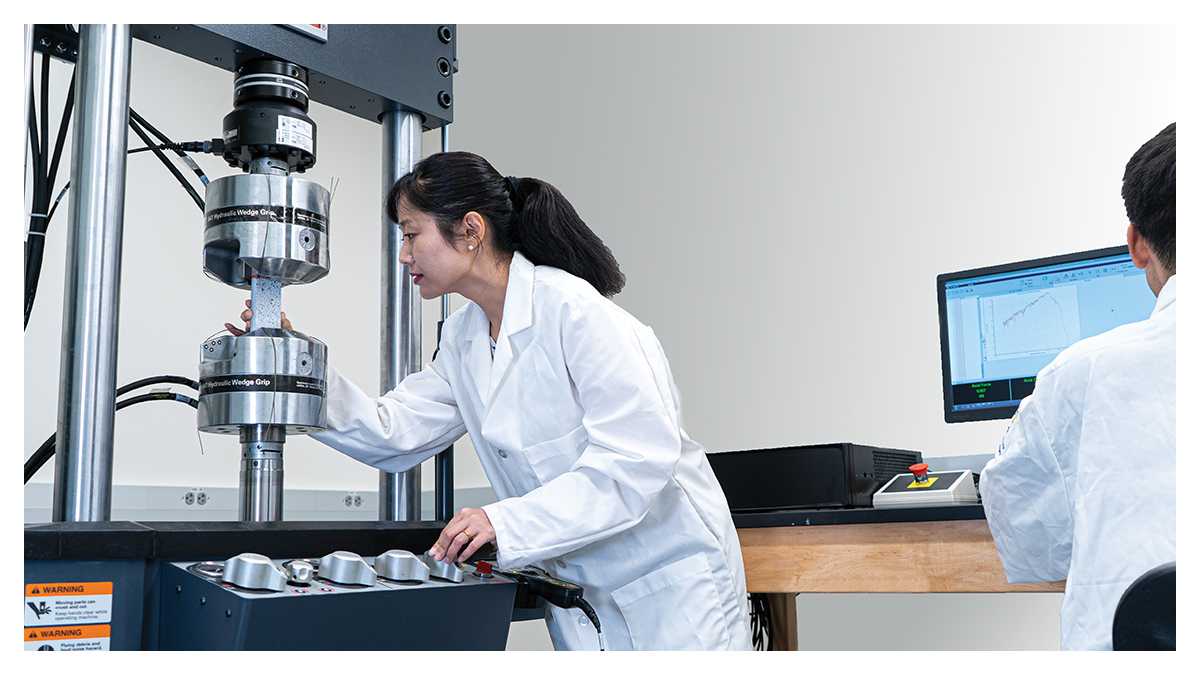
In her lab, Li and her Ph.D. student conduct tests on samples of next-generation infrastructure materials.
Li is also involved in accelerating bridge construction. The California Department of Transportation and the Federal Highway Administration wanted to explore faster ways to build bridges, which is a relatively slow process that often causes disruptions to traffic and the environment. The approach is to prefabricate bridge segments at a plant and assemble them on site. A major challenge has been obtaining durable and seismically resilient connections between the prefabricated components. Li’s group is tackling this challenge by developing ultra-high-strength and ultra-high-ductility cementitious – or cement-like – materials for constructing the connections. This allows for faster construction, high quality of structural members, minimal onsite falsework and improved durability, which leads to lower maintenance and life-cycle costs.
Another project underway has Li working with the California Energy Commission, developing innovative materials and manufacturing solutions for land-based and offshore wind energy generation. With the next generation of wind turbines expected to be significantly taller than the current ones, the problem again is how to construct such ultra-tall, highly loaded structures. The idea is to move away from large prefabricated sections that become impossible to transport to wind farms and move toward an on-site, automated additive manufacturing method. To enable this, Li is developing innovative 3D-printable concrete and additive manufacturing methods using large robot arms – similar to the ones used in automotive production lines. The new 3D-printable concrete must be suited for rapid additive manufacturing without conventional formworks while still maintaining its high strength and durability for highly loaded structures. According to Li, this new approach can potentially unlock up to 3,700 gigawatts of new land-based and offshore wind energy technical resource potential, with significantly reduced capital costs.
Onward and Upward
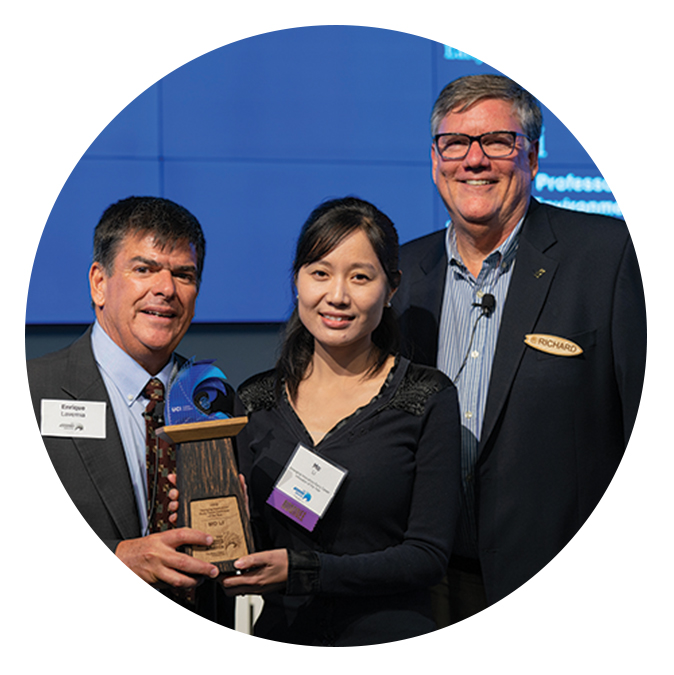
Li with Enrique Lavernia, UCI provost and executive vice chancellor, and Richard Sudek, UCI chief innovation officer and executive director of UCI Beall Applied Innovation, at the 2019 UCI Innovator of the Year Awards ceremony.
Li, who received the 2019 Emerging Innovation/Early Career Innovator of the Year award, is passionate about making an impact with her work by changing the materials that will make the structures of tomorrow safer, smarter and more resilient.
“Changing the materials opens new doors of tremendous possibilities,” said Li.
Materials influence how humans interact with the world, and from her office and lab on the UC Irvine campus, Li works toward changing the world one material at a time.
Learn more about Li’s areas of research.
- Ethan Perez / UCI Beall Applied Innovation